Picture this: You’re cruising down the highway in your sleek electric vehicle, enjoying the smooth, quiet ride. 🚗⚡ But have you ever wondered why your electric motor purrs along so effortlessly, seemingly immune to the frequent maintenance demands of its gasoline-powered counterparts? The answer lies in the ingenious simplicity and robustness of electric motors.
In a world where time is precious and efficiency is key, electric motors are revolutionizing the way we think about vehicle maintenance. Gone are the days of regular oil changes, spark plug replacements, and timing belt adjustments. Electric motors offer a tantalizing promise: less time in the shop and more time on the road. But what makes these powerhouses so low-maintenance? From their streamlined design to their advanced cooling systems, electric motors are built to last—and to keep you moving with minimal fuss.
In this post, we’ll dive into the seven key reasons why electric motors require less maintenance, uncovering the technological marvels that make them a game-changer in the automotive world and beyond. Get ready to discover how simplified designs, durable components, and smart features are reshaping our expectations of vehicle upkeep and paving the way for a more efficient, cost-effective future.
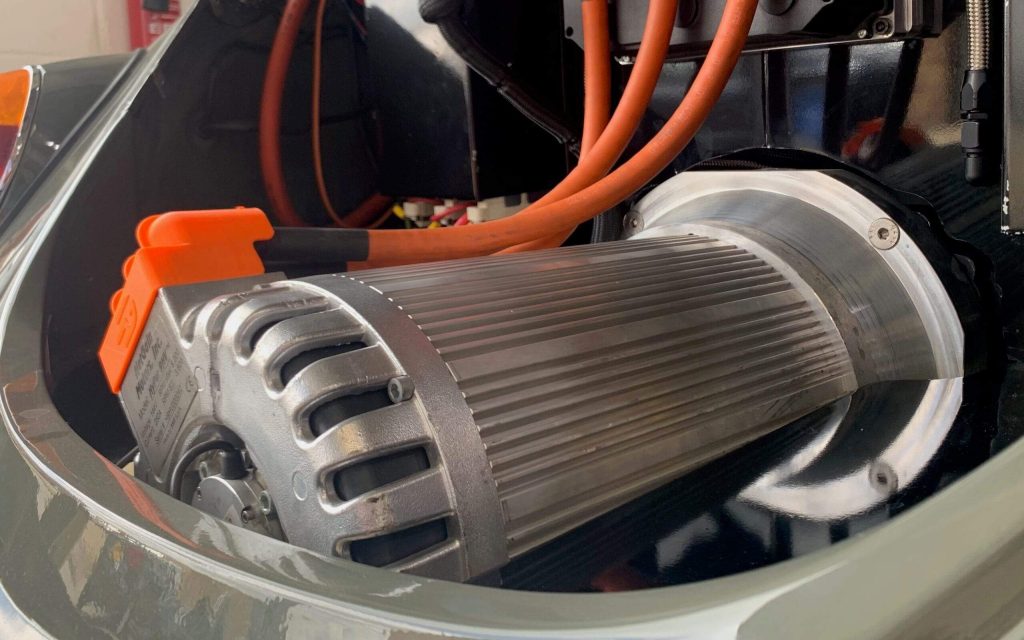
Simplified Design of Electric Motors
Fewer Moving Parts
Electric motors boast a streamlined design with significantly fewer moving parts compared to traditional combustion engines. This simplicity translates to reduced maintenance needs and increased reliability.
Component | Electric Motor | Combustion Engine |
---|---|---|
Moving Parts | 20-30 | 200+ |
Maintenance Frequency | Low | High |
Absence of Combustion System
Without a complex combustion system, electric motors eliminate the need for:
- Fuel injectors
- Spark plugs
- Valves
- Exhaust systems
This absence greatly reduces potential failure points and maintenance requirements, contributing to the overall efficiency and longevity of electric motors.
Durability of Electric Motor Components
Long-lasting Brushless Motors
Brushless motors significantly enhance electric motor durability. Unlike traditional brushed motors, they eliminate wear-prone components, resulting in:
- Extended lifespan
- Reduced maintenance needs
- Higher efficiency
- Lower heat generation
Feature | Brushed Motors | Brushless Motors |
---|---|---|
Lifespan | Shorter | Longer |
Maintenance | Regular | Minimal |
Efficiency | Lower | Higher |
Robust Copper Windings
Copper windings in electric motors offer superior conductivity and durability. These high-quality components contribute to:
- Improved power efficiency
- Better heat dissipation
- Longer motor life
- Reduced maintenance requirements
Reduced Wear and Tear
Lower Operating Temperatures
Electric motors operate at lower temperatures compared to combustion engines, significantly reducing wear and tear. This temperature difference impacts longevity:
Engine Type | Average Operating Temperature |
---|---|
Electric | 70-100°C (158-212°F) |
Combustion | 200-250°C (392-482°F) |
Smoother Power Delivery
Electric motors provide smoother power delivery, minimizing stress on components. Benefits include:
- Instant torque
- Fewer moving parts
- Reduced friction
This smooth operation contributes to the overall durability and reduced maintenance needs of electric motors.
Advanced Cooling Systems
Efficient Heat Dissipation
Electric motors employ advanced cooling systems for optimal performance. These systems efficiently dissipate heat, preventing overheating and reducing wear on components.
Cooling Method | Benefits |
---|---|
Air Cooling | Simple, low cost |
Liquid Cooling | Higher efficiency |
Hybrid Systems | Best of both |
Liquid Cooling Advantages
Liquid cooling offers superior heat management compared to traditional air cooling:
- Higher heat capacity
- More uniform temperature distribution
- Allows for compact motor design
Smart Maintenance Features
Self-diagnostic Capabilities
Electric motors equipped with smart maintenance features offer significant advantages:
- Real-time performance monitoring
- Early problem detection
- Automated fault reporting
- Improved reliability
Predictive Maintenance Algorithms
These algorithms analyze motor data to predict potential issues:
Benefit | Description |
---|---|
Reduced downtime | Anticipates failures before they occur |
Optimized maintenance | Schedules service based on actual wear |
Extended lifespan | Prevents catastrophic failures |
Smart features enable proactive maintenance, minimizing unexpected breakdowns and optimizing motor performance over time.
Environmental Factors
No Exposure to Harmful Emissions
Electric motors operate without producing harmful emissions, creating a cleaner environment for the motor itself. This absence of pollutants reduces the risk of contamination and degradation of motor components, contributing to their longevity and reduced maintenance needs.
Cleaner Operating Environment
Factor | Electric Motors | Combustion Engines |
---|---|---|
Emissions | None | Exhaust gases |
Contaminants | Minimal | Oil, fuel residues |
Air Quality | Clean | Polluted |
A cleaner operating environment means fewer particles and contaminants that could potentially damage the motor’s internal components, leading to extended lifespan and decreased maintenance requirements.
Cost-Effective Upkeep
Lower Frequency of Servicing
Electric motors require servicing less often than traditional combustion engines, leading to significant cost savings. Here’s a comparison of maintenance frequencies:
Engine Type | Oil Changes | Filter Replacements | Major Service |
---|---|---|---|
Electric | None | Every 2-3 years | Every 5 years |
Combustion | Every 3-6 months | Every 1-2 years | Every 2-3 years |
Fewer Replacement Parts Needed
Electric motors have fewer moving parts, reducing the need for replacements. This simplicity translates to:
- Lower parts inventory costs
- Decreased downtime for repairs
- Minimized risk of component failures
Electric motors stand out as a low-maintenance powerhouse in the world of machinery. Their simplified design, durable components, and reduced wear and tear contribute significantly to their longevity and reliability. Advanced cooling systems and smart maintenance features further enhance their efficiency and ease of upkeep.
The environmental benefits and cost-effectiveness of electric motors make them an attractive choice for various applications. As technology continues to advance, we can expect even more innovations in electric motor design, leading to even lower maintenance requirements and higher performance. Embracing electric motors not only streamlines maintenance processes but also paves the way for a more sustainable and efficient future in industrial and consumer applications.
Leave a Reply