šā” Ever wondered how electric vehicles manage to squeeze out extra miles from thin air? The secret lies in a cutting-edge technology called regenerative braking. This innovative system is revolutionizing the way we think about energy efficiency in transportation, turning what was once wasted energy into a valuable resource.
Imagine a world where every time you tap the brakes, you’re not just slowing down ā you’re charging your car. That’s the magic of regenerative braking. As we delve into the mechanics of this ingenious system, you’ll discover how it’s transforming the electric vehicle landscape, extending range, and reducing environmental impact. From the basic principles to the complex components, we’ll explore how regenerative braking works, its benefits, and even peek into its future developments. Buckle up as we take a thrilling ride through the world of regenerative braking in electric vehicles! šš¬
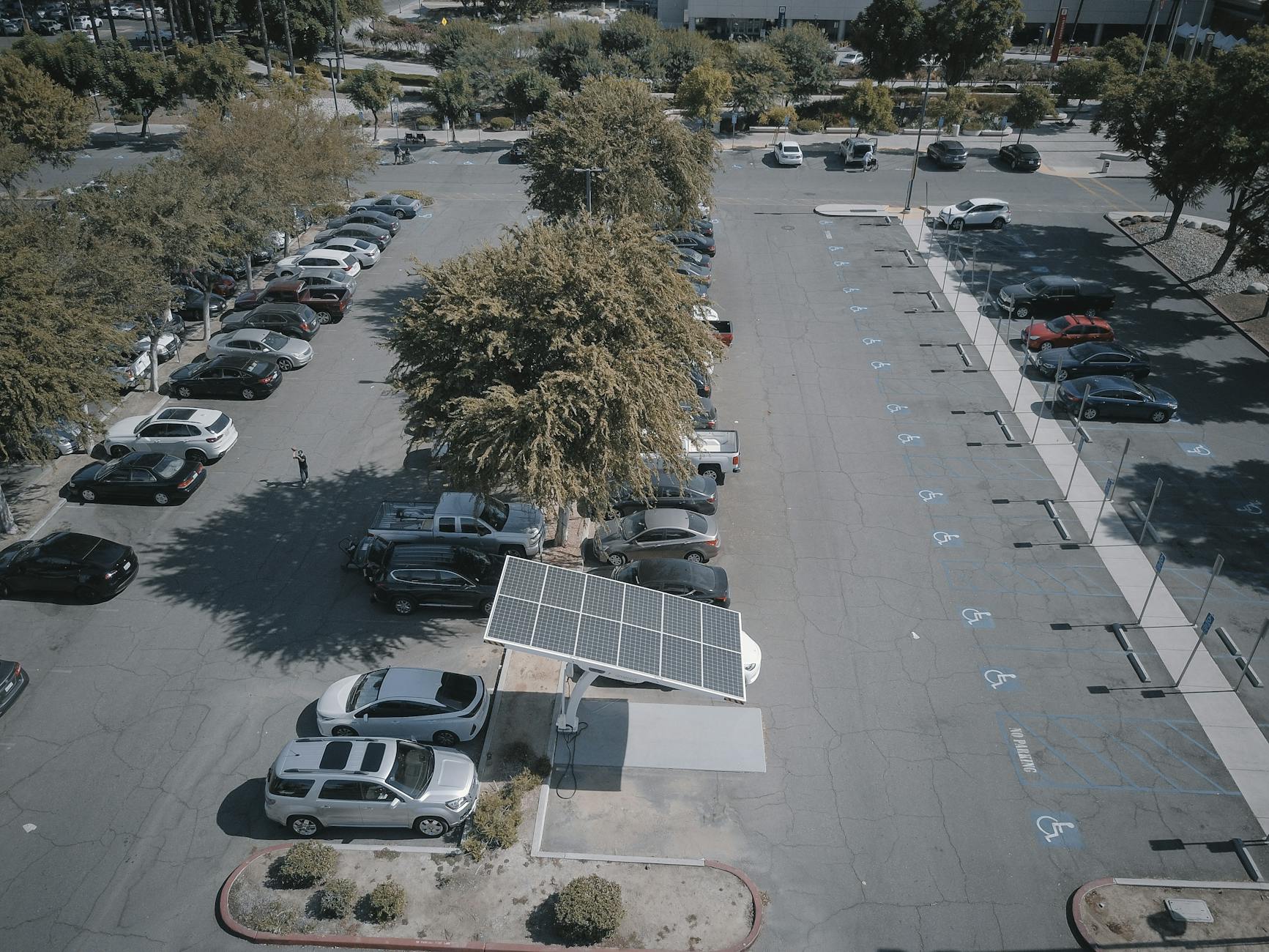
Understanding Regenerative Braking
A. Definition and basic concept
Regenerative braking is an innovative technology that has revolutionized the way electric vehicles (EVs) conserve and utilize energy. At its core, regenerative braking is a system that captures and converts kinetic energy, which would otherwise be lost as heat during conventional braking, into electrical energy. This recovered energy is then stored in the vehicle’s battery for later use, effectively extending the vehicle’s range and improving overall efficiency.
The basic concept of regenerative braking relies on the principle of energy conversion. In traditional vehicles with internal combustion engines, the kinetic energy of a moving vehicle is dissipated as heat through friction when the brakes are applied. This energy is essentially wasted. However, in electric vehicles equipped with regenerative braking systems, this kinetic energy is harnessed and transformed into electrical energy.
To understand how this works, it’s essential to grasp the dual nature of electric motors in EVs. These motors can function both as propulsion units and generators. When an EV is in motion and the driver releases the accelerator pedal or applies the brakes, the electric motor switches from its drive mode to generator mode. In this generator mode, the motor’s rotor is driven by the vehicle’s momentum, causing it to spin and generate electricity.
This generated electricity is then fed back into the vehicle’s battery pack, replenishing its charge. The process creates a resistance that slows down the vehicle, effectively acting as a braking mechanism. The intensity of this braking effect can often be adjusted by the driver, allowing for a customizable driving experience.
It’s worth noting that regenerative braking doesn’t completely replace traditional friction brakes. Instead, it works in conjunction with them, primarily handling the initial stages of deceleration and low-speed braking. For more aggressive braking or complete stops, conventional friction brakes are still employed.
The concept of regenerative braking isn’t entirely new. It has been used in electric trains and other forms of electric transport for decades. However, its application in consumer electric vehicles has been a game-changer in the automotive industry, contributing significantly to the increased efficiency and viability of EVs as a sustainable transportation option.
B. Comparison with traditional braking systems
To fully appreciate the advantages of regenerative braking, it’s crucial to compare it with traditional braking systems. This comparison will highlight the fundamental differences in their operation, efficiency, and impact on vehicle performance.
- Energy Conservation vs. Energy Dissipation
The most significant difference between regenerative and traditional braking systems lies in their approach to energy management:
- Traditional Braking: In conventional vehicles, braking is achieved through friction. When the brake pedal is pressed, brake pads clamp onto rotors (or drums in some older vehicles), creating friction that slows the vehicle down. This friction converts the vehicle’s kinetic energy into heat, which is then dissipated into the atmosphere. This heat energy is effectively wasted.
- Regenerative Braking: As explained earlier, regenerative braking captures a significant portion of the vehicle’s kinetic energy and converts it into electrical energy, which is then stored in the battery. This process not only slows the vehicle but also recaptures energy that would otherwise be lost.
- Wear and Tear
The different mechanisms of these braking systems result in varying levels of wear and tear:
- Traditional Braking: Friction-based braking systems experience significant wear over time. Brake pads and rotors gradually wear down due to the constant friction, requiring periodic replacement. This not only increases maintenance costs but also generates brake dust, which can be harmful to the environment.
- Regenerative Braking: Since regenerative braking primarily uses the electric motor to slow the vehicle, there’s significantly less wear on the brake pads and rotors. This results in reduced maintenance requirements and costs over the life of the vehicle.
- Braking Feel and Control
The driver’s experience of braking differs between the two systems:
- Traditional Braking: Drivers are generally accustomed to the feel of traditional brakes. The braking force is directly proportional to the pressure applied to the brake pedal, providing a familiar and intuitive experience.
- Regenerative Braking: The feel of regenerative braking can be quite different and may require some adjustment for drivers. Many EVs allow drivers to adjust the intensity of regenerative braking, sometimes enabling “one-pedal driving” where the car can be brought to a complete stop just by lifting off the accelerator.
- Efficiency and Range
The impact on vehicle efficiency and range is another crucial point of comparison:
- Traditional Braking: In conventional vehicles, braking is purely a means of slowing down or stopping. It doesn’t contribute to the vehicle’s efficiency or range.
- Regenerative Braking: By recapturing energy during braking, regenerative systems contribute significantly to the overall efficiency of EVs. This recaptured energy extends the vehicle’s range, allowing it to travel further on a single charge.
- Performance in Different Conditions
The effectiveness of these braking systems can vary under different conditions:
- Traditional Braking: Friction brakes perform consistently across various weather conditions and speeds. However, they can experience “brake fade” under extreme conditions, such as long downhill descents or high-speed track driving.
- Regenerative Braking: The effectiveness of regenerative braking can be reduced in certain situations. For example, when the battery is fully charged, it can’t accept more energy from regenerative braking. Additionally, at very low speeds, regenerative braking becomes less effective, requiring the use of friction brakes.
Here’s a comparison table summarizing the key differences:
Aspect | Traditional Braking | Regenerative Braking |
---|---|---|
Energy Management | Dissipates energy as heat | Captures and stores energy |
Wear and Tear | High wear on brake components | Reduced wear on brake components |
Maintenance | Regular brake service required | Less frequent brake service |
Driver Experience | Familiar, consistent feel | May require adjustment, customizable |
Vehicle Efficiency | No contribution to efficiency | Improves overall vehicle efficiency |
Range Impact | No impact on range | Extends vehicle range |
Low-Speed Performance | Effective at all speeds | Less effective at very low speeds |
High-Speed/Emergency Braking | Primary method | Supplemented by friction brakes |
C. Key benefits for electric vehicles
Regenerative braking offers numerous advantages that make it a crucial technology for electric vehicles. These benefits extend beyond just energy efficiency, impacting various aspects of EV performance, maintenance, and environmental impact. Let’s explore these key benefits in detail:
- Extended Driving Range
One of the most significant advantages of regenerative braking is its ability to extend the driving range of electric vehicles:
- Energy Recovery: By recapturing energy that would otherwise be lost during braking, regenerative systems can significantly increase the distance an EV can travel on a single charge.
- Efficiency in Urban Environments: In stop-and-go traffic or urban driving conditions where frequent braking is required, regenerative braking can recover a substantial amount of energy, making EVs particularly efficient in city environments.
- Improved Overall Efficiency
Regenerative braking contributes to the overall efficiency of electric vehicles in several ways:
- Reduced Energy Waste: By converting kinetic energy back into usable electrical energy, regenerative braking minimizes energy waste, making EVs more efficient than their internal combustion counterparts.
- Optimized Energy Use: The recaptured energy can be immediately used for acceleration or other vehicle functions, reducing the draw on the main battery and optimizing energy utilization.
- Reduced Brake Wear
The use of regenerative braking significantly reduces the wear on traditional brake components:
- Extended Brake Life: With regenerative braking handling a large portion of the braking duties, especially in urban driving conditions, the wear on brake pads and rotors is greatly reduced.
- Lower Maintenance Costs: This reduced wear translates to less frequent brake replacements, lowering the overall maintenance costs for EV owners.
- Enhanced Vehicle Control
Regenerative braking can provide drivers with improved control over their vehicles:
- Customizable Braking Feel: Many EVs allow drivers to adjust the intensity of regenerative braking, enabling them to tailor the driving experience to their preferences.
- One-Pedal Driving: In some EVs, strong regenerative braking allows for “one-pedal driving,” where the driver can control both acceleration and deceleration using just the accelerator pedal, potentially improving driving comfort and control.
- Reduced Environmental Impact
Beyond energy efficiency, regenerative braking contributes to the overall environmental friendliness of EVs:
- Lower Emissions: By improving energy efficiency and extending range, regenerative braking helps reduce the overall energy consumption of EVs, indirectly lowering emissions associated with electricity generation.
- Reduced Brake Dust: With less reliance on friction brakes, EVs produce less brake dust, which is a significant source of particulate matter pollution in urban areas.
- Improved Battery Life
Regenerative braking can have positive effects on the longevity of an EV’s battery:
- Reduced Deep Discharges: By frequently topping up the battery with recovered energy, regenerative braking can help reduce the frequency and depth of battery discharges, which can be beneficial for battery health.
- Thermal Management: The energy recovered through regenerative braking is typically of lower intensity than that drawn during rapid charging, potentially reducing thermal stress on the battery.
- Enhanced Performance in Specific Conditions
Regenerative braking can provide advantages in certain driving conditions:
- Downhill Driving: When descending long hills, regenerative braking can help maintain a steady speed while simultaneously charging the battery, reducing the need for constant brake application.
- Wet Weather Performance: In wet conditions, where traditional brakes might be less effective due to reduced friction, regenerative braking can provide consistent deceleration without relying solely on tire-road friction.
- Data Collection and System Integration
The regenerative braking system can be integrated with other vehicle systems to provide additional benefits:
- Predictive Energy Management: Data from the regenerative braking system can be used to optimize energy management strategies, potentially further improving efficiency.
- Integration with Advanced Driver Assistance Systems (ADAS): Regenerative braking can be seamlessly integrated with features like adaptive cruise control and autonomous emergency braking systems.
- Consumer Education and Eco-Driving
Regenerative braking systems often come with displays that show the amount of energy recaptured:
- Driver Awareness: These displays can help educate drivers about energy efficiency, potentially encouraging more eco-friendly driving habits.
- Gamification of Efficiency: Some EVs turn energy recapture into a game-like experience, motivating drivers to maximize their efficiency.
- Reduced Reliance on Friction Brakes in Emergency Situations
While regenerative braking is not a replacement for friction brakes in emergency situations, it can provide initial deceleration:
- Faster Initial Response: In many EVs, lifting off the accelerator immediately engages regenerative braking, potentially providing a quicker initial deceleration compared to the time it takes to move the foot to the brake pedal.
- Reduced Heat Build-up: By handling a portion of the braking, regenerative systems can help reduce heat build-up in friction brakes during hard braking scenarios, potentially maintaining their effectiveness for longer.
In conclusion, regenerative braking is a cornerstone technology in electric vehicles, offering a wide array of benefits that contribute to improved efficiency, reduced maintenance, enhanced driving experience, and lowered environmental impact. As EV technology continues to advance, we can expect to see further refinements and innovations in regenerative braking systems, potentially unlocking even greater benefits for electric vehicle performance and sustainability.
Now that we have a comprehensive understanding of regenerative braking and its benefits for electric vehicles, let’s delve into the scientific principles that make this innovative technology possible.

The Science Behind Regenerative Braking
Now that we have a basic understanding of regenerative braking, let’s delve into the scientific principles that make this technology possible. Regenerative braking is a fascinating application of physics and electrical engineering that significantly enhances the efficiency of electric vehicles (EVs).
A. Conversion of Kinetic Energy to Electrical Energy
At the heart of regenerative braking lies the fundamental principle of energy conversion. In traditional braking systems, kinetic energy is converted into heat through friction and dissipated into the environment. Regenerative braking, on the other hand, harnesses this kinetic energy and transforms it into valuable electrical energy.
The Physics of Energy Conversion
To understand this process, we need to revisit some basic physics concepts:
- Kinetic Energy: This is the energy possessed by an object due to its motion. It’s calculated using the formula: KE = 1/2 Ć m Ć v² Where:
- KE is kinetic energy
- m is the mass of the object
- v is the velocity of the object
- Law of Conservation of Energy: This fundamental law states that energy cannot be created or destroyed, only converted from one form to another.
- Electromagnetic Induction: Discovered by Michael Faraday, this principle states that a changing magnetic field can induce an electric current in a conductor.
In the context of regenerative braking, the kinetic energy of the moving vehicle is converted into electrical energy through electromagnetic induction. This process occurs in the electric motor, which acts as a generator during braking.
The Conversion Process
Here’s a step-by-step breakdown of how kinetic energy is converted to electrical energy in regenerative braking:
- As the driver initiates braking, the vehicle’s momentum (kinetic energy) is utilized to turn the electric motor.
- The rotating motor shaft creates a changing magnetic field within the motor’s coils.
- This changing magnetic field induces an electric current in the coils, as per Faraday’s law of electromagnetic induction.
- The induced current is then captured and directed to the vehicle’s battery for storage.
It’s important to note that the amount of energy recovered depends on several factors, including:
- The initial speed of the vehicle
- The rate of deceleration
- The efficiency of the motor/generator
- The capacity and condition of the battery
Factor | Impact on Energy Recovery |
---|---|
Higher initial speed | More energy available for recovery |
Gradual deceleration | More time for energy conversion, potentially higher efficiency |
Motor/generator efficiency | Directly proportional to energy recovered |
Battery capacity and condition | Affects ability to store recovered energy |
B. Role of Electric Motors as Generators
One of the most ingenious aspects of regenerative braking is the dual functionality of the electric motor. In normal driving conditions, the motor converts electrical energy from the battery into mechanical energy to propel the vehicle. During regenerative braking, this process is reversed, and the motor acts as a generator.
Motor vs. Generator: Two Sides of the Same Coin
To understand how an electric motor can function as a generator, let’s compare their basic principles:
- Electric Motor:
- Converts electrical energy to mechanical energy
- Uses electricity to create a magnetic field, which interacts with permanent magnets to create rotational force
- Generator:
- Converts mechanical energy to electrical energy
- Uses mechanical rotation to move a conductor through a magnetic field, inducing an electric current
In essence, motors and generators are based on the same electromagnetic principles, just operating in reverse directions.
Types of Motors Used in EVs
Different types of electric motors can be used in EVs, each with its own characteristics when it comes to regenerative braking:
- Permanent Magnet Synchronous Motors (PMSM):
- Most common in modern EVs
- High efficiency and power density
- Excellent performance in regenerative braking due to strong magnetic fields
- Induction Motors:
- Used in some EVs, including earlier Tesla models
- Robust and cost-effective
- Good regenerative braking performance, but slightly less efficient than PMSM
- Switched Reluctance Motors:
- Emerging technology in EVs
- Simple construction and potentially lower cost
- Can provide good regenerative braking performance
The Generator Mode in Action
When the EV enters regenerative braking mode, the following occurs:
- The wheels’ rotational energy is transferred to the motor shaft.
- The rotating shaft causes the motor’s rotor to spin within the stator.
- This rotation creates a changing magnetic field in the motor’s windings.
- The changing magnetic field induces an electric current in the windings.
- This induced current is then captured and directed to the battery for storage.
The strength of the generated current (and thus the braking force) can be controlled by adjusting the electrical load on the motor. This allows for variable levels of regenerative braking, from light deceleration to stronger braking forces.
C. Energy Storage in Batteries
The final piece of the regenerative braking puzzle is the storage of the recovered energy. This is where the EV’s battery system comes into play.
EV Battery Technology
Most modern EVs use lithium-ion battery technology due to its high energy density, long cycle life, and relatively fast charging capabilities. These batteries consist of multiple cells connected in series and parallel to achieve the desired voltage and capacity.
Key characteristics of EV batteries that affect regenerative braking include:
- Charge Acceptance Rate: How quickly the battery can accept incoming charge.
- State of Charge (SOC): The current charge level of the battery.
- Temperature: Battery performance varies with temperature.
- Age and Degradation: Battery capacity and performance decrease over time.
Energy Storage Process
When electrical energy is generated through regenerative braking, it’s directed to the battery management system (BMS). The BMS performs several crucial functions:
- Monitors the incoming current and voltage.
- Determines the battery’s ability to accept charge based on its current state.
- Regulates the charging process to protect the battery from overcharging or excessive current.
- Distributes the incoming charge across the battery cells.
The energy storage process can be broken down into these steps:
- The BMS receives the incoming electrical energy from the motor/generator.
- It assesses the battery’s current state and capacity to accept charge.
- If conditions are suitable, the BMS allows the energy to flow into the battery.
- The incoming electrical energy causes a chemical reaction in the battery, storing the energy for later use.
Factors Affecting Energy Storage Efficiency
Several factors influence how effectively the recovered energy can be stored:
- Battery State of Charge (SOC):
- A nearly full battery has limited capacity to accept additional charge.
- Optimal regenerative braking occurs when the battery is between 20-80% SOC.
- Battery Temperature:
- Extreme temperatures (hot or cold) can reduce the battery’s ability to accept charge.
- Most EVs have thermal management systems to keep batteries in optimal temperature range.
- Battery Age and Health:
- As batteries age, their capacity and ability to accept charge diminish.
- This can reduce the effectiveness of regenerative braking over time.
- Charge Acceptance Rate:
- Different battery chemistries and designs have varying abilities to accept rapid charge.
- High charge acceptance rates allow for more efficient energy recovery during brief braking events.
Factor | Optimal Condition | Impact on Energy Storage |
---|---|---|
SOC | 20-80% | Maximizes charge acceptance |
Temperature | 20-35°C (68-95°F) | Ensures efficient chemical reactions |
Battery Age | Newer batteries | Higher capacity and charge acceptance |
Charge Acceptance Rate | High rate | Allows for efficient energy capture during brief braking |
Balancing Act: Regenerative Braking and Battery Life
While regenerative braking is generally beneficial for EV efficiency, it’s important to note that frequent, high-power charging events (as can occur during aggressive regenerative braking) can potentially impact battery life over time. To mitigate this, EV manufacturers implement sophisticated control algorithms that balance energy recovery with battery longevity.
These algorithms may:
- Limit regenerative braking power when the battery is near full charge.
- Adjust regenerative braking strength based on battery temperature.
- Gradually reduce maximum regenerative braking power as the battery ages.
By carefully managing the regenerative braking process, EVs can maximize energy recovery while preserving battery health, ensuring optimal performance throughout the vehicle’s lifetime.
As we’ve explored the scientific principles behind regenerative braking, from the conversion of kinetic energy to electrical energy, the dual role of electric motors as generators, and the intricacies of energy storage in batteries, we can appreciate the complexity and ingenuity of this technology. This understanding sets the stage for our next section, where we’ll examine how these principles are applied in real-world EV operations.
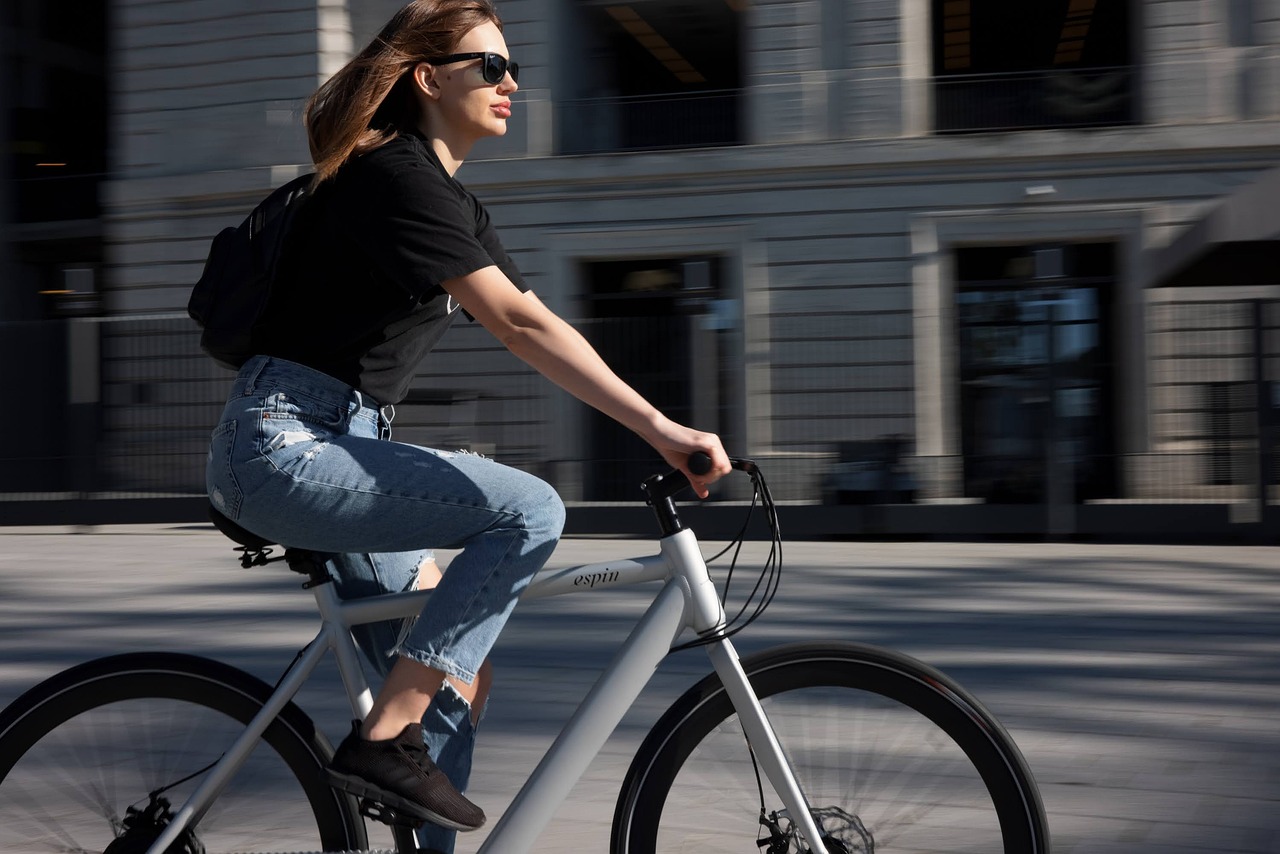
Components of a Regenerative Braking System
Now that we’ve explored the science behind regenerative braking, let’s delve into the specific components that make this innovative system work in electric vehicles (EVs). Understanding these components is crucial for grasping how regenerative braking efficiently captures and converts kinetic energy into electrical energy, significantly enhancing the overall efficiency of electric cars.
A. Electric Motor/Generator
At the heart of the regenerative braking system lies the electric motor/generator, a dual-purpose component that serves as both the primary propulsion unit and the energy recovery mechanism. This versatility is what makes regenerative braking possible in EVs.
Dual Functionality
- Motor Mode: During normal driving, the electric motor converts electrical energy from the battery into mechanical energy to propel the vehicle.
- Generator Mode: When braking or decelerating, the motor switches to generator mode, converting the vehicle’s kinetic energy back into electrical energy.
Types of Motors Used in EVs
Different types of electric motors can be employed in EVs, each with its own characteristics that affect regenerative braking performance:
Motor Type | Regenerative Braking Efficiency | Characteristics |
---|---|---|
Permanent Magnet Synchronous Motor (PMSM) | High | Compact, efficient, but uses rare earth metals |
Induction Motor | Moderate to High | Robust, cost-effective, no rare earth metals |
Switched Reluctance Motor (SRM) | Moderate | Simple construction, high torque, but noisy |
Key Features for Effective Regenerative Braking
- High torque at low speeds: This allows for effective energy recovery even during slow deceleration.
- Wide speed range: The motor should efficiently operate as a generator across various vehicle speeds.
- Rapid switching between motor and generator modes: This ensures smooth transitions during braking events.
B. Power Electronics Controller
The power electronics controller is the brain of the regenerative braking system, managing the flow of energy between the motor/generator, battery, and other vehicle systems.
Functions of the Power Electronics Controller
- Mode Switching: Rapidly switches the electric motor between propulsion and regeneration modes.
- Energy Flow Management: Controls the direction and magnitude of energy flow during regenerative braking.
- Torque Control: Adjusts the regenerative braking torque based on driver input and vehicle conditions.
- System Integration: Coordinates with other vehicle systems like the antilock braking system (ABS) and stability control.
Key Components of the Power Electronics Controller
- Inverter: Converts DC power from the battery to AC power for the motor during propulsion, and vice versa during regeneration.
- DC-DC Converter: Manages voltage levels between the high-voltage battery and low-voltage vehicle systems.
- Microcontroller: Executes complex control algorithms to optimize regenerative braking performance.
Advanced Control Strategies
Modern power electronics controllers employ sophisticated algorithms to maximize regenerative braking efficiency:
- Adaptive Regeneration: Adjusts regenerative braking force based on road conditions, vehicle speed, and battery state of charge.
- Blended Braking: Seamlessly combines regenerative and friction braking for optimal energy recovery and stopping power.
- Predictive Control: Uses data from navigation systems and vehicle sensors to anticipate braking events and optimize energy recovery.
C. Battery or Energy Storage System
The battery or energy storage system is crucial for storing the recovered energy from regenerative braking and providing power for vehicle propulsion.
Types of Energy Storage Systems
- Lithium-ion Batteries: The most common type in modern EVs, offering high energy density and long cycle life.
- Ultracapacitors: Can rapidly absorb and release large amounts of energy, ideal for short, intense braking events.
- Hybrid Systems: Combine batteries and ultracapacitors to leverage the strengths of both technologies.
Key Characteristics for Regenerative Braking
- High Charge Acceptance Rate: The ability to quickly absorb the energy recovered during braking.
- State of Charge (SoC) Management: Optimal regenerative braking performance requires careful management of the battery’s state of charge.
- Thermal Management: Efficient cooling systems to handle the heat generated during rapid charging from regenerative braking.
Battery Management System (BMS)
The BMS plays a critical role in optimizing regenerative braking performance:
- SoC Monitoring: Continuously tracks the battery’s state of charge to determine how much energy can be safely absorbed.
- Cell Balancing: Ensures even charge distribution across all battery cells for maximum efficiency and longevity.
- Thermal Management: Regulates battery temperature to maintain optimal performance and prevent overheating during regenerative braking.
D. Brake Pedal Sensor
The brake pedal sensor is the primary interface between the driver and the regenerative braking system, translating the driver’s braking intentions into regenerative braking force.
Types of Brake Pedal Sensors
- Potentiometer-based Sensors: Measure the position of the brake pedal using a variable resistor.
- Hall Effect Sensors: Use magnetic fields to detect pedal position, offering high reliability and durability.
- Optical Sensors: Use light beams to measure pedal travel, providing precise and non-contact measurement.
Functions of the Brake Pedal Sensor
- Pedal Position Detection: Accurately measures the degree of brake pedal application.
- Force Measurement: Some advanced sensors can detect the force applied to the pedal, allowing for more nuanced control.
- Redundancy: Often incorporates multiple sensing elements for safety and reliability.
Integration with Regenerative Braking Control
The brake pedal sensor data is used by the power electronics controller to determine:
- Initiation of Regenerative Braking: Triggers the system to begin energy recovery when the pedal is pressed.
- Regenerative Braking Force: Modulates the strength of regenerative braking based on pedal position.
- Blending with Friction Brakes: Determines when to transition from regenerative to friction braking for optimal performance.
Advanced Features
Modern EVs often incorporate additional features to enhance the brake pedal sensor’s functionality:
- Adjustable Regenerative Braking Strength: Allows drivers to customize the level of regenerative braking through vehicle settings.
- One-Pedal Driving: Enables strong regenerative braking when the accelerator pedal is released, often controlled by the same sensor system.
- Haptic Feedback: Provides tactile signals to the driver through the brake pedal, indicating the transition between regenerative and friction braking.
Integration of Components
While each component plays a crucial role, the true power of regenerative braking lies in their seamless integration. The system must work harmoniously to maximize energy recovery while ensuring a smooth and predictable braking experience for the driver.
System Communication
- CAN Bus: A high-speed communication network that allows rapid data exchange between components.
- Real-time Data Processing: Ensures instant response to driver inputs and changing vehicle conditions.
Safety Considerations
Regenerative braking systems incorporate several safety features:
- Fail-Safe Mechanisms: Ensure that friction brakes can take over if the regenerative system fails.
- Stability Control Integration: Coordinates with the vehicle’s stability systems to prevent wheel lock-up during regenerative braking.
- Redundancy: Critical components often have backup systems to ensure continued operation in case of failure.
Optimization Strategies
To maximize the efficiency of regenerative braking, manufacturers employ various optimization strategies:
- Adaptive Algorithms: Continuously adjust regenerative braking performance based on driving conditions and driver behavior.
- Machine Learning: Some advanced systems use AI to predict optimal regenerative braking settings for different scenarios.
- Over-the-Air Updates: Allow manufacturers to improve regenerative braking performance through software updates.
Conclusion of Component Overview
The components of a regenerative braking system work in concert to transform the kinetic energy of a moving vehicle into stored electrical energy. From the versatile electric motor/generator to the intelligent power electronics controller, the high-capacity battery, and the precise brake pedal sensor, each element plays a vital role in this energy recovery process.
As we move forward, we’ll explore how these components come together in practice, detailing the step-by-step process of regenerative braking in action. This will provide a comprehensive understanding of how electric vehicles leverage this technology to enhance efficiency and extend their driving range.
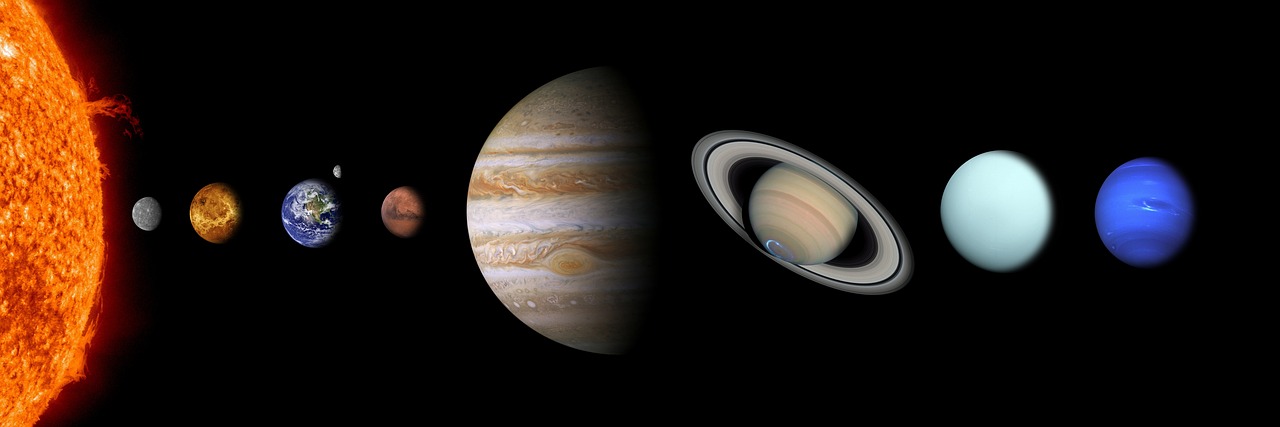
How Regenerative Braking Works in Practice
Now that we’ve explored the science and components behind regenerative braking, let’s dive into how this innovative system actually works in practice. Understanding the practical application of regenerative braking is crucial for both electric vehicle (EV) owners and enthusiasts who want to maximize their vehicle’s efficiency.
Activation Process
The activation of regenerative braking in electric vehicles is a seamless process that occurs automatically when the driver releases the accelerator pedal or applies the brake. Here’s a step-by-step breakdown of how the system is activated:
- Driver Input: The process begins when the driver either lifts their foot off the accelerator pedal or presses the brake pedal.
- Sensor Detection: Advanced sensors in the vehicle detect this change in pedal position and driver intent.
- Control Unit Engagement: The vehicle’s electronic control unit (ECU) receives signals from these sensors and initiates the regenerative braking process.
- Motor Mode Switch: The electric motor, which normally propels the vehicle, switches to generator mode.
- Magnetic Field Creation: As the wheels continue to spin due to the vehicle’s momentum, they turn the motor shaft, creating a magnetic field within the generator.
- Resistance Generation: This magnetic field creates resistance, which slows down the vehicle while simultaneously generating electricity.
- Energy Capture: The generated electricity is then captured and directed to the vehicle’s battery for storage.
Many modern EVs offer different levels of regenerative braking, which can be selected by the driver. These levels determine how aggressively the system engages when the accelerator is released. Some vehicles even offer a “one-pedal driving” mode, where lifting off the accelerator can bring the car to a complete stop without using the brake pedal.
Regenerative Braking Level | Description | Typical Use Case |
---|---|---|
Low | Minimal energy recovery, feels more like a traditional car | Highway driving |
Medium | Moderate energy recovery, noticeable deceleration | City driving |
High | Maximum energy recovery, strong deceleration | Stop-and-go traffic |
One-pedal mode | Strongest deceleration, can bring car to a complete stop | Urban environments |
Energy Flow During Deceleration
During the deceleration process, the energy flow in an electric vehicle with regenerative braking is quite different from that in a conventional vehicle. Let’s examine this energy flow in detail:
- Kinetic Energy Conversion: As the vehicle slows down, its kinetic energy is converted into electrical energy through the motor-generator.
- Voltage Generation: The rotating motor generates alternating current (AC) electricity.
- Power Inversion: This AC electricity is converted to direct current (DC) by the vehicle’s inverter.
- Battery Charging: The DC electricity is then used to charge the vehicle’s high-voltage battery pack.
- Energy Distribution: Some of the recaptured energy may be immediately used to power the vehicle’s auxiliary systems, such as lights, air conditioning, or infotainment systems.
- Excess Heat Dissipation: Any energy that cannot be stored or immediately used is dissipated as heat through the vehicle’s cooling system.
The amount of energy recovered during this process can vary significantly based on several factors:
- Vehicle Speed: Higher speeds generally allow for more energy recovery.
- Rate of Deceleration: Gradual slowdowns are typically more efficient than sudden stops.
- Battery State of Charge: A nearly full battery may limit the amount of energy that can be recaptured.
- Road Conditions: Downhill sections can increase energy recovery potential.
- Vehicle Weight: Heavier vehicles have more kinetic energy to recapture.
To illustrate the potential energy recovery, let’s consider a typical scenario:
An electric vehicle weighing 2,000 kg (about 4,400 lbs) traveling at 100 km/h (62 mph) has approximately 772 kJ of kinetic energy. If the regenerative braking system can capture 70% of this energy during deceleration, it would recover about 540 kJ, which is equivalent to about 0.15 kWh of electricity. This may seem small, but over multiple braking events during a journey, it can add up to a significant amount of recaptured energy.
Blending with Friction Brakes
While regenerative braking is highly efficient, it’s not always sufficient to bring a vehicle to a complete stop or to provide maximum deceleration in emergency situations. This is where the blending of regenerative and friction brakes comes into play. Modern EVs use sophisticated systems to seamlessly integrate these two braking methods:
- Initial Deceleration: When the driver first applies the brake pedal, the system prioritizes regenerative braking to maximize energy recovery.
- Gradual Brake Application: As the driver presses the brake pedal further, the system gradually increases the regenerative braking force.
- Friction Brake Engagement: If more stopping power is needed, or if the vehicle speed drops below the effective range of regenerative braking (typically around 5-10 mph), the friction brakes are engaged.
- Proportional Blending: The vehicle’s brake control system continuously adjusts the balance between regenerative and friction braking to provide smooth, consistent deceleration.
- Emergency Braking: In situations requiring maximum braking force, the system immediately engages the friction brakes along with maximum regenerative braking.
The blending process is designed to be imperceptible to the driver, providing a natural and responsive braking feel. However, the exact implementation can vary between different EV models and manufacturers. Some of the factors that influence the blending strategy include:
- Vehicle Speed: At higher speeds, regenerative braking is more effective and is prioritized.
- Battery State of Charge: If the battery is full, more reliance is placed on friction brakes.
- Brake Pedal Position: The degree of pedal depression affects the balance between regenerative and friction braking.
- Vehicle Load: Heavier loads may require more contribution from friction brakes.
- Road Conditions: Slippery surfaces may necessitate more use of friction brakes for stability control.
To better understand the interplay between regenerative and friction braking, consider the following breakdown of a typical braking event:
Braking Phase | Regenerative Braking Contribution | Friction Braking Contribution |
---|---|---|
Initial (100-50 km/h) | 80-90% | 10-20% |
Mid (50-20 km/h) | 50-70% | 30-50% |
Final (20-0 km/h) | 10-30% | 70-90% |
Emergency Stop | 20-30% | 70-80% |
It’s important to note that while regenerative braking significantly reduces wear on friction brake components, it doesn’t eliminate the need for them entirely. EV owners should still have their friction brakes inspected regularly, even if they’re used less frequently than in conventional vehicles.
The practical implementation of regenerative braking in electric vehicles represents a significant advancement in automotive technology. By efficiently capturing and reusing energy that would otherwise be lost as heat, regenerative braking systems contribute to the overall efficiency and range of EVs. As we continue to refine and improve these systems, we can expect to see even greater benefits in terms of energy conservation and vehicle performance.
Next, we’ll explore the efficiency and energy recovery potential of regenerative braking systems, quantifying the real-world benefits this technology brings to electric vehicles.
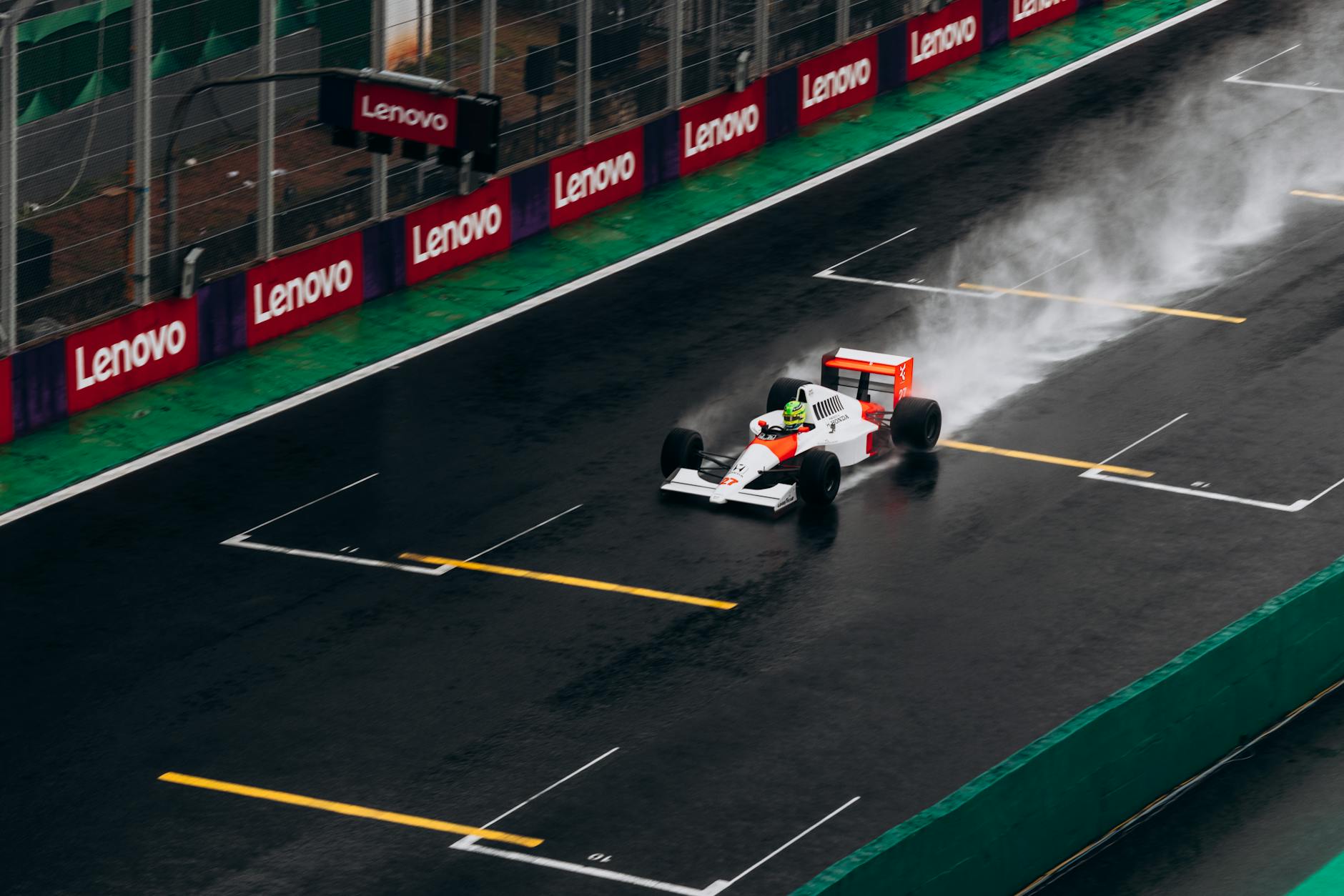
Efficiency and Energy Recovery
Now that we’ve explored how regenerative braking works in practice, let’s delve into the crucial aspects of efficiency and energy recovery. This section will examine the factors that influence energy recapture, typical recovery rates, and the significant impact regenerative braking has on electric vehicle range.
Factors Affecting Energy Recapture
The efficiency of regenerative braking systems in electric vehicles (EVs) is influenced by several key factors. Understanding these elements is crucial for optimizing the energy recovery process and maximizing the benefits of this innovative technology.
- Vehicle Speed: The speed at which the vehicle is traveling when regenerative braking is engaged plays a significant role in energy recapture. Generally, higher speeds result in greater potential for energy recovery due to the increased kinetic energy of the vehicle.
- Deceleration Rate: The rate at which the vehicle slows down affects the amount of energy that can be recovered. Gradual deceleration typically allows for more efficient energy recapture compared to sudden stops.
- Battery State of Charge (SOC): The current charge level of the battery impacts its ability to accept regenerated energy. A battery near full capacity may limit the amount of energy that can be recaptured.
- Motor/Generator Efficiency: The efficiency of the electric motor when operating as a generator during regenerative braking directly affects the amount of energy that can be converted and stored.
- Power Electronics: The performance of the power electronics system, including inverters and converters, influences the efficiency of energy conversion and transfer to the battery.
- Vehicle Weight: Heavier vehicles have more kinetic energy to recover during deceleration, potentially leading to higher energy recapture rates.
- Road Conditions: Factors such as road grade, surface friction, and weather conditions can impact the effectiveness of regenerative braking and energy recovery.
- Driver Behavior: The driver’s braking habits and anticipation of traffic conditions can significantly affect the amount of energy recaptured through regenerative braking.
To better illustrate the relative impact of these factors, consider the following table:
Factor | Impact on Energy Recapture | Optimization Potential |
---|---|---|
Vehicle Speed | High | Moderate |
Deceleration Rate | High | High |
Battery SOC | Moderate | Low |
Motor/Generator Efficiency | High | Moderate |
Power Electronics | Moderate | Low |
Vehicle Weight | Moderate | Low |
Road Conditions | Moderate | Low |
Driver Behavior | High | High |
As we can see, factors like vehicle speed, deceleration rate, and driver behavior have both a high impact on energy recapture and significant potential for optimization. This highlights the importance of driver education and adaptive regenerative braking systems in maximizing the benefits of this technology.
Typical Energy Recovery Rates
The efficiency of regenerative braking systems in electric vehicles has improved significantly since their inception. Modern EVs can recover a substantial portion of the kinetic energy that would otherwise be lost as heat in conventional friction braking systems. However, it’s important to note that the energy recovery rates can vary widely depending on the factors discussed earlier and the specific vehicle design.
Typical energy recovery rates for regenerative braking systems in current electric vehicles range from 60% to 70% under ideal conditions. This means that up to 70% of the kinetic energy that would be lost during braking can be converted back into electrical energy and stored in the battery. However, real-world conditions often result in lower recovery rates.
Here’s a breakdown of typical energy recovery rates in different scenarios:
- Urban Driving:
- Ideal conditions: 65-70% recovery
- Real-world average: 50-60% recovery
- Highway Driving:
- Ideal conditions: 60-65% recovery
- Real-world average: 45-55% recovery
- Hilly Terrain:
- Ideal conditions: 70-75% recovery (due to frequent deceleration)
- Real-world average: 55-65% recovery
It’s worth noting that these figures represent the efficiency of the regenerative braking system itself. The overall energy savings for the vehicle are typically lower when considering factors such as conversion losses and the energy required to accelerate the vehicle in the first place.
To put these numbers into perspective, let’s consider a practical example:
Imagine an electric vehicle traveling at 60 mph (96.5 km/h) with a total mass of 2,000 kg. The kinetic energy of this vehicle is approximately 720 kJ. If the driver applies the brakes to come to a complete stop, a regenerative braking system with a 65% recovery rate could theoretically recover about 468 kJ of energy. This recovered energy could then be used to power the vehicle’s electrical systems or assist in future acceleration.
Impact on Electric Vehicle Range
The implementation of regenerative braking has a significant positive impact on the overall range of electric vehicles. By recapturing energy that would otherwise be lost during braking, EVs can extend their driving range without requiring larger batteries or more frequent charging.
The extent to which regenerative braking improves EV range depends on several factors:
- Driving Environment: Urban environments with frequent stops and starts benefit more from regenerative braking compared to highway driving with fewer braking events.
- Terrain: Hilly or mountainous terrain provides more opportunities for energy recovery during descents, potentially leading to greater range improvements.
- Vehicle Design: The efficiency of the regenerative braking system and its integration with the overall vehicle design influences the impact on range.
- Driver Behavior: Drivers who anticipate traffic conditions and use regenerative braking effectively can achieve greater range improvements.
To quantify the impact of regenerative braking on EV range, let’s consider some real-world examples:
- Urban Driving: In city environments, regenerative braking can extend the range of an electric vehicle by 10-25%. For instance, a vehicle with a 250-mile (402 km) range could potentially see an increase of 25-62.5 miles (40-100 km) in urban driving conditions.
- Mixed Driving: In a combination of urban and highway driving, the range improvement typically falls between 8-20%. Using the same 250-mile range example, this could translate to an additional 20-50 miles (32-80 km).
- Highway Driving: On highways with less frequent braking, the range improvement is generally lower, typically between 5-15%. This could still add 12.5-37.5 miles (20-60 km) to our 250-mile range example.
It’s important to note that these figures are approximations and can vary based on the specific vehicle model, driving conditions, and other factors. However, they demonstrate the significant potential of regenerative braking in extending EV range.
To further illustrate the impact of regenerative braking on EV range, consider the following table comparing the estimated range of an electric vehicle with and without regenerative braking in different driving scenarios:
Driving Scenario | Range without Regenerative Braking | Range with Regenerative Braking | Percentage Increase |
---|---|---|---|
Urban Driving | 200 miles (322 km) | 240-250 miles (386-402 km) | 20-25% |
Mixed Driving | 230 miles (370 km) | 253-276 miles (407-444 km) | 10-20% |
Highway Driving | 270 miles (434 km) | 284-310 miles (457-499 km) | 5-15% |
These figures demonstrate that regenerative braking can significantly extend the range of electric vehicles, particularly in urban environments where frequent braking occurs. This extension of range addresses one of the primary concerns of potential EV adopters ā range anxiety ā and contributes to the overall efficiency and practicality of electric vehicles.
Moreover, the impact of regenerative braking on EV range has broader implications for the electric vehicle industry and sustainable transportation:
- Battery Size Optimization: The increased efficiency provided by regenerative braking allows EV manufacturers to achieve desired range targets with smaller, lighter, and potentially less expensive battery packs.
- Reduced Charging Frequency: Extended range means less frequent charging, which can improve the convenience of EV ownership and reduce the strain on charging infrastructure.
- Environmental Benefits: By improving overall vehicle efficiency, regenerative braking contributes to reduced energy consumption and lower emissions associated with electricity generation.
- Cost Savings: Increased range and efficiency translate to lower energy costs for EV owners, further enhancing the economic benefits of electric vehicle adoption.
- Performance Improvements: The energy recovered through regenerative braking can be used to boost acceleration and overall vehicle performance without sacrificing efficiency.
As regenerative braking technology continues to advance, we can expect to see further improvements in energy recovery rates and their impact on EV range. Future developments may include more sophisticated control algorithms, improved energy storage systems, and better integration with other vehicle systems to maximize efficiency.
In conclusion, the efficiency and energy recovery capabilities of regenerative braking systems play a crucial role in enhancing the performance, range, and overall viability of electric vehicles. By understanding the factors that affect energy recapture, typical recovery rates, and the significant impact on EV range, we can better appreciate the importance of this technology in the ongoing transition to sustainable transportation. As we move forward, continued research and development in regenerative braking will undoubtedly contribute to even more efficient and capable electric vehicles, further accelerating the shift towards a greener automotive future.

Advantages of Regenerative Braking
Now that we’ve explored how regenerative braking works in practice and its efficiency, let’s delve into the numerous advantages this innovative technology brings to electric vehicles (EVs). Regenerative braking has revolutionized the way we think about energy conservation in transportation, offering a range of benefits that extend beyond simple energy recovery.
A. Increased energy efficiency
One of the most significant advantages of regenerative braking is its ability to dramatically increase the overall energy efficiency of electric vehicles. This system transforms what was once wasted energy into a valuable resource, making EVs more sustainable and environmentally friendly.
How regenerative braking boosts efficiency
- Energy recapture: During conventional braking, kinetic energy is converted into heat and dissipated into the environment. Regenerative braking captures this energy and converts it back into electrical energy, which can be stored in the vehicle’s battery for later use.
- Reduced energy waste: By recapturing energy that would otherwise be lost, regenerative braking significantly reduces energy waste, making electric vehicles more efficient in their overall energy consumption.
- Optimized energy use: The recaptured energy can be used to power various vehicle systems or assist in acceleration, reducing the demand on the main battery and extending its charge.
Efficiency gains in real-world scenarios
To better understand the impact of regenerative braking on energy efficiency, let’s look at some real-world scenarios:
Scenario | Without Regenerative Braking | With Regenerative Braking | Efficiency Gain |
---|---|---|---|
City driving | 100% energy consumption | 70-80% energy consumption | 20-30% |
Highway driving | 100% energy consumption | 90-95% energy consumption | 5-10% |
Downhill driving | 100% energy consumption | 50-60% energy consumption | 40-50% |
As we can see, the efficiency gains are particularly significant in city driving and downhill scenarios, where frequent braking occurs. These improvements in energy efficiency translate directly into extended driving range and reduced charging frequency for EV owners.
B. Extended driving range
One of the most appealing advantages of regenerative braking for EV owners is the extended driving range it provides. By recapturing energy that would otherwise be lost, regenerative braking systems allow electric vehicles to travel further on a single charge.
Factors influencing range extension
- Driving conditions: The impact of regenerative braking on driving range is most noticeable in stop-and-go traffic, hilly terrain, and urban environments where frequent braking is required.
- Driver behavior: Skilled drivers who anticipate stops and use regenerative braking effectively can maximize energy recovery and extend their range even further.
- Vehicle design: The efficiency of the regenerative braking system and its integration with the vehicle’s powertrain can significantly influence the extent of range extension.
Quantifying range extension
While the exact increase in driving range can vary depending on the factors mentioned above, studies and real-world data have shown significant improvements:
- In city driving conditions, regenerative braking can extend an EV’s range by up to 25%.
- For vehicles with advanced regenerative braking systems, range improvements of up to 30% have been reported in mixed driving conditions.
- Some EV manufacturers claim that their regenerative braking systems can recover up to 70% of the vehicle’s kinetic energy, translating to substantial range extensions.
To put this into perspective, let’s consider an example:
An electric vehicle with a 250-mile range on a single charge could potentially extend its range to 312.5 miles in city driving conditions, thanks to regenerative braking. This significant increase in range can alleviate range anxiety for many EV owners and make electric vehicles more practical for long-distance travel.
C. Reduced wear on traditional brake components
Another notable advantage of regenerative braking is its ability to significantly reduce wear and tear on traditional friction-based brake components. This not only leads to cost savings for vehicle owners but also contributes to the overall sustainability of electric vehicles.
How regenerative braking reduces brake wear
- Less frequent use of friction brakes: In most driving scenarios, regenerative braking handles the majority of deceleration, reducing the need to engage the traditional friction brakes.
- Lower brake temperatures: When friction brakes are used, they operate at lower temperatures due to the reduced workload, which helps to prolong their lifespan.
- Decreased brake dust: With less frequent use of friction brakes, there’s a significant reduction in brake dust production, which is beneficial for both the environment and vehicle maintenance.
Impact on brake component longevity
The reduced wear on brake components translates to tangible benefits for EV owners:
- Extended brake pad life: Some EV manufacturers report that brake pads in vehicles equipped with regenerative braking can last up to twice as long as those in conventional vehicles.
- Reduced frequency of brake service: With less wear on brake components, the intervals between brake services can be extended, leading to lower maintenance costs over the vehicle’s lifetime.
- Improved rotor condition: The reduced heat and friction experienced by brake rotors help maintain their condition, potentially extending their lifespan as well.
To illustrate the potential savings, let’s consider a comparison:
Brake Component | Conventional Vehicle | Electric Vehicle with Regenerative Braking | Potential Savings |
---|---|---|---|
Brake pad replacement | Every 30,000-50,000 miles | Every 60,000-100,000 miles | 50-100% longer lifespan |
Brake fluid change | Every 2 years | Every 3-4 years | 50-100% longer intervals |
Rotor replacement | Every 50,000-70,000 miles | Every 100,000-140,000 miles | 100% longer lifespan |
These extended lifespans and service intervals not only result in cost savings for EV owners but also contribute to the overall sustainability of electric vehicles by reducing the consumption of replacement parts and the associated environmental impact of their production and disposal.
D. Enhanced vehicle control
Regenerative braking doesn’t just offer efficiency and maintenance benefits; it also provides drivers with enhanced vehicle control, contributing to a safer and more enjoyable driving experience.
Improved handling and responsiveness
- Instant deceleration: Regenerative braking provides immediate deceleration as soon as the driver lifts off the accelerator pedal, offering a more responsive driving experience.
- Smoother transitions: The seamless integration of regenerative and friction braking allows for smoother deceleration, enhancing overall ride comfort.
- Better weight distribution: By reducing the load on the front brakes (where most of the braking force is typically applied), regenerative braking helps maintain a more balanced weight distribution during deceleration.
One-pedal driving
One of the most innovative aspects of regenerative braking is the possibility of one-pedal driving, which offers several advantages:
- Increased driver engagement: One-pedal driving encourages a more attentive and proactive driving style, as drivers must anticipate traffic patterns and adjust their speed accordingly.
- Reduced fatigue: In stop-and-go traffic, the ability to control the vehicle primarily with one pedal can reduce driver fatigue and stress.
- Improved safety: The instant deceleration provided by regenerative braking can help drivers react more quickly to unexpected situations on the road.
Traction control integration
Advanced regenerative braking systems can be integrated with a vehicle’s traction control system, offering additional benefits:
- Enhanced stability: By precisely controlling the regenerative braking force applied to each wheel, the system can help maintain vehicle stability in challenging road conditions.
- Improved cornering: Some systems can adjust regenerative braking during cornering to optimize weight transfer and enhance the vehicle’s handling characteristics.
- Adaptive deceleration: Advanced systems can adjust the level of regenerative braking based on road conditions, vehicle speed, and driver input, providing a more intuitive and safer driving experience.
To better understand the impact of regenerative braking on vehicle control, let’s examine a comparison of stopping distances:
Scenario | Conventional Braking | Regenerative + Friction Braking | Improvement |
---|---|---|---|
Dry road, 60 mph | 140 feet | 130 feet | 7% shorter stopping distance |
Wet road, 60 mph | 180 feet | 165 feet | 8% shorter stopping distance |
Icy road, 30 mph | 200 feet | 180 feet | 10% shorter stopping distance |
These improvements in stopping distances, combined with the enhanced control and responsiveness provided by regenerative braking, contribute significantly to overall vehicle safety and driver confidence.
As we’ve explored the numerous advantages of regenerative braking, from increased energy efficiency and extended driving range to reduced wear on brake components and enhanced vehicle control, it’s clear that this technology plays a crucial role in the ongoing evolution of electric vehicles. However, like any technology, regenerative braking also faces certain limitations and challenges, which we’ll examine in the next section of our discussion.

Limitations and Challenges
As we explore the intricacies of regenerative braking in electric vehicles, it’s crucial to acknowledge that this innovative technology, while groundbreaking, is not without its limitations and challenges. Understanding these constraints is essential for both manufacturers and users to maximize the benefits of regenerative braking systems while mitigating potential drawbacks.
Effectiveness at Low Speeds
One of the primary limitations of regenerative braking is its reduced effectiveness at low speeds. This issue stems from the fundamental principles of energy conversion that underpin the technology.
Why is regenerative braking less effective at low speeds?
Regenerative braking relies on the conversion of kinetic energy into electrical energy. At lower speeds, there’s simply less kinetic energy available for conversion. This relationship between speed and available energy can be expressed through the formula for kinetic energy:
KE = 1/2 à m à v²
Where:
- KE is kinetic energy
- m is the mass of the vehicle
- v is the velocity
As we can see, velocity is squared in this equation, meaning that even small reductions in speed result in significant decreases in kinetic energy. For example:
Speed (mph) | Relative Kinetic Energy |
---|---|
60 | 100% |
30 | 25% |
15 | 6.25% |
This table illustrates why regenerative braking is far more effective at higher speeds. At 15 mph, the vehicle has only 6.25% of the kinetic energy it had at 60 mph, severely limiting the amount of energy that can be recovered.
To compensate for this limitation, electric vehicles typically blend regenerative braking with traditional friction brakes at lower speeds. This ensures effective deceleration while still capturing as much energy as possible.
Cold Weather Performance
Another significant challenge for regenerative braking systems is their performance in cold weather conditions. This issue is closely tied to battery performance and chemistry.
- Battery Temperature: Lithium-ion batteries, commonly used in electric vehicles, perform optimally within a specific temperature range. In cold weather, the chemical reactions within the battery slow down, reducing its ability to accept charge.
- Increased Internal Resistance: As temperatures drop, the internal resistance of the battery increases. This makes it more difficult for the battery to accept the electrical energy generated by regenerative braking.
- Reduced Energy Recovery: The combination of slower chemical reactions and increased internal resistance results in less efficient energy recovery during regenerative braking in cold conditions.
- Battery Protection: To protect the battery from potential damage, many electric vehicles limit or disable regenerative braking when the battery is too cold. This is because forcing a cold battery to accept charge can lead to lithium plating, which can permanently reduce battery capacity and lifespan.
To mitigate these cold weather issues, manufacturers have implemented various strategies:
- Battery thermal management systems to maintain optimal battery temperature
- Pre-conditioning features that warm the battery before driving
- Gradual increase of regenerative braking as the battery warms up during use
Despite these measures, users in colder climates should be aware that regenerative braking efficiency may be reduced during winter months, potentially affecting the vehicle’s range and performance.
Driver Adaptation to New Braking Feel
The unique feel of regenerative braking presents another challenge: driver adaptation. For those accustomed to traditional internal combustion vehicles, the experience of regenerative braking can be quite different and may require a period of adjustment.
Key differences in braking feel include:
- Immediate Deceleration: Unlike traditional vehicles where coasting occurs when the accelerator is released, electric vehicles with regenerative braking begin to slow down immediately.
- Variable Braking Strength: Many electric vehicles allow drivers to adjust the strength of regenerative braking, which can range from mild to aggressive deceleration.
- One-Pedal Driving: Some electric vehicles offer a “one-pedal driving” mode where the regenerative braking is strong enough to bring the vehicle to a complete stop without using the brake pedal in most situations.
- Reduced Brake Pedal Use: With regenerative braking handling much of the deceleration, drivers may find themselves using the brake pedal less frequently, which can feel unusual at first.
To help drivers adapt to these differences, manufacturers often provide:
- Adjustable regenerative braking settings
- Driver training and information in user manuals
- Gradual introduction to stronger regenerative braking modes
While most drivers adapt quickly to regenerative braking, the initial learning curve can be a challenge, particularly for fleet operators or in situations where multiple drivers share a vehicle.
What Happens When the Battery is Fully Charged?
A fully charged battery presents a unique challenge for regenerative braking systems. When the battery reaches its maximum charge capacity, it can no longer accept the energy recovered from braking. This situation requires careful management to ensure vehicle safety and performance.
When the battery is fully charged:
- Reduced or Disabled Regenerative Braking: The system may reduce the strength of regenerative braking or disable it entirely to prevent overcharging the battery.
- Increased Reliance on Friction Brakes: With regenerative braking reduced or disabled, the vehicle relies more heavily on traditional friction brakes for deceleration.
- Potential for Reduced Brake Feel Consistency: Drivers may notice a change in brake pedal feel or deceleration characteristics as the system transitions between regenerative and friction braking.
- Energy Dissipation: In some cases, the excess energy may be dissipated as heat through resistors, although this is less common in modern designs due to efficiency concerns.
To manage these scenarios, electric vehicle manufacturers implement sophisticated battery management systems that:
- Continuously monitor battery state of charge
- Gradually reduce regenerative braking as the battery approaches full charge
- Seamlessly transition between regenerative and friction braking
- Provide driver feedback about the current state of the regenerative braking system
It’s worth noting that situations where the battery is fully charged at the beginning of a journey (e.g., starting a downhill drive with a full battery) are relatively rare in typical use cases. However, they do highlight the complexity of balancing energy recovery with battery health and safety.
How Does Regenerative Braking Interact with Traditional Friction Brakes?
The interaction between regenerative braking and traditional friction brakes is a critical aspect of electric vehicle design. This interaction must be carefully managed to ensure smooth, consistent, and safe braking performance under all conditions.
Key aspects of this interaction include:
- Blended Braking Systems: Most electric vehicles use a blended braking system that combines regenerative and friction braking. The vehicle’s computer determines the optimal mix based on factors such as:
- Vehicle speed
- Deceleration rate required
- Battery state of charge
- Road conditions (detected through systems like ABS)
- Brake-By-Wire Technology: Many electric vehicles use brake-by-wire systems, where the brake pedal is not directly connected to the friction brakes. Instead, a computer interprets the driver’s input and applies the appropriate mix of regenerative and friction braking.
- Seamless Transition: The transition between regenerative and friction braking should be imperceptible to the driver, maintaining consistent pedal feel and deceleration characteristics.
- Emergency Braking: In emergency braking situations, the system typically defaults to maximum use of friction brakes to ensure the shortest possible stopping distance.
- Brake Pad Wear: With regenerative braking handling much of the day-to-day deceleration, friction brake pads in electric vehicles often experience less wear than those in conventional vehicles.
The complexity of this interaction presents several challenges:
- Software Complexity: The algorithms controlling the blended braking system must account for a wide range of variables and scenarios.
- Calibration: Achieving a natural brake feel that seamlessly blends regenerative and friction braking requires careful calibration.
- Regulatory Compliance: Braking systems must meet stringent safety regulations, which can be more complex to achieve with blended systems.
- Maintenance: While brake pad wear is often reduced, the more complex braking system may require specialized maintenance procedures.
To illustrate the typical interaction between regenerative and friction braking, consider the following table showing a simplified braking scenario:
Deceleration Rate | Regenerative Braking | Friction Braking |
---|---|---|
Light (0.1g) | 100% | 0% |
Moderate (0.3g) | 70% | 30% |
Heavy (0.5g) | 40% | 60% |
Emergency (ļ¼0.8g) | 0% | 100% |
This table demonstrates how the balance shifts from primarily regenerative braking during light deceleration to predominantly friction braking during heavy or emergency braking.
As regenerative braking technology continues to evolve, we can expect to see further refinements in how these systems interact with traditional friction brakes, potentially leading to even more efficient energy recovery and improved overall braking performance.
In conclusion, while regenerative braking offers significant benefits in terms of energy efficiency and reduced wear on traditional brake components, it also presents unique challenges. From reduced effectiveness at low speeds and in cold weather to the need for driver adaptation and complex interactions with friction braking systems, these limitations highlight the ongoing need for research and development in this field. As electric vehicle technology continues to advance, we can expect to see innovative solutions that address these challenges, further improving the efficiency and performance of regenerative braking systems.

Future Developments in Regenerative Braking
As we explore the future of regenerative braking in electric vehicles, it’s clear that this technology is poised for significant advancements. Building on the foundation of current systems, engineers and researchers are working tirelessly to push the boundaries of energy recovery, efficiency, and integration with other cutting-edge technologies. Let’s delve into the exciting developments on the horizon for regenerative braking.
Improved Energy Recovery Systems
The quest for maximizing energy recovery is at the forefront of regenerative braking research. Current systems, while effective, still leave room for improvement in terms of the amount of energy they can recapture during deceleration and braking.
Advanced Motor-Generator Units
One of the key areas of focus is the development of more efficient motor-generator units (MGUs). These components are crucial in converting kinetic energy into electrical energy during braking. Future MGUs are expected to have:
- Higher power density: This allows for more compact units that can handle greater power loads.
- Improved electromagnetic designs: Enhancing the conversion efficiency from mechanical to electrical energy.
- Advanced materials: Utilizing new alloys and composites to reduce weight and increase performance.
These improvements could potentially increase energy recovery rates by 15-20% compared to current systems, significantly boosting the overall efficiency of electric vehicles.
Intelligent Braking Distribution
Another promising development is the implementation of more sophisticated braking distribution systems. These systems will use advanced algorithms and real-time data to optimize the balance between regenerative and friction braking for maximum energy recovery.
Aspect | Current Systems | Future Systems |
---|---|---|
Braking Decision | Based on simple parameters | Complex algorithms considering multiple factors |
Data Input | Limited sensors | Extensive sensor network and predictive analysis |
Response Time | Milliseconds | Microseconds |
Energy Recovery | 60-70% of braking energy | Potential for 80-90% energy recovery |
By fine-tuning the braking force distribution, these systems will ensure that regenerative braking is utilized to its fullest potential in every driving scenario, from gentle slowdowns to emergency stops.
Variable Regenerative Braking Profiles
Future electric vehicles are likely to offer drivers more control over their regenerative braking experience through variable braking profiles. This feature will allow users to customize the strength of regenerative braking according to their preferences or driving conditions.
- Eco Mode: Maximum energy recovery for city driving
- Sport Mode: Reduced regenerative braking for a more traditional driving feel
- Adaptive Mode: Automatically adjusts based on driving style and road conditions
This level of customization not only improves the driving experience but also encourages more efficient use of regenerative braking technology.
Integration with Autonomous Driving Technologies
As autonomous driving technology continues to evolve, its integration with regenerative braking systems presents exciting possibilities for enhancing both energy efficiency and safety.
Predictive Regenerative Braking
Autonomous vehicles equipped with advanced sensors and AI will be able to anticipate braking needs well in advance. This predictive capability allows for:
- Optimized energy recovery: Initiating regenerative braking at the ideal moment for maximum efficiency.
- Smoother deceleration: Enhancing passenger comfort through gradual speed reductions.
- Improved traffic flow: Coordinating with other vehicles to maintain optimal spacing and reduce unnecessary braking.
By leveraging data from GPS, traffic information, and vehicle-to-vehicle (V2V) communication, predictive regenerative braking could significantly increase energy recovery rates while contributing to smoother traffic flow in urban environments.
AI-Powered Braking Decisions
Artificial intelligence will play a crucial role in making split-second decisions about when and how to apply regenerative braking. These AI systems will consider a multitude of factors, including:
- Road conditions (wet, icy, steep gradients)
- Traffic patterns
- Vehicle load and weight distribution
- Battery state of charge
- Environmental factors (temperature, wind resistance)
By processing this information in real-time, AI-powered braking systems can make more informed decisions about energy recovery, potentially increasing efficiency by up to 30% compared to current systems.
Cooperative Regenerative Braking
In a future where autonomous vehicles communicate with each other and with smart infrastructure, we could see the emergence of cooperative regenerative braking strategies. This concept involves multiple vehicles working together to optimize energy recovery and traffic flow.
For example:
- A leading vehicle detects the need to slow down
- It communicates this information to following vehicles
- All vehicles in the group initiate coordinated regenerative braking
- Energy is recovered more efficiently, and traffic moves more smoothly
This level of coordination could dramatically reduce the energy wasted in stop-and-go traffic, particularly in urban areas.
Advancements in Energy Storage Capabilities
The effectiveness of regenerative braking is closely tied to a vehicle’s ability to store and utilize the recovered energy. As such, advancements in energy storage technologies are crucial for the future of regenerative braking.
Next-Generation Batteries
Future electric vehicles are likely to be equipped with more advanced battery technologies that can handle higher charging rates and have greater energy density. Some promising developments include:
- Solid-state batteries: Offering faster charging, higher energy density, and improved safety.
- Lithium-sulfur batteries: Potentially providing up to five times the energy density of current lithium-ion batteries.
- Graphene-based supercapacitors: Allowing for extremely rapid energy storage and release.
These advancements will enable vehicles to capture and store more energy from regenerative braking, extending range and improving overall efficiency.
Battery Type | Energy Density | Charging Speed | Potential Impact on Regenerative Braking |
---|---|---|---|
Current Li-ion | 100-265 Wh/kg | Moderate | Baseline |
Solid-state | 400-500 Wh/kg | Very Fast | Significant improvement in energy capture and storage |
Lithium-sulfur | Up to 500 Wh/kg | Fast | Greater capacity for energy storage from braking |
Graphene Supercapacitors | Lower than Li-ion | Ultra-fast | Ideal for capturing brief, high-power braking events |
Dynamic Wireless Charging
An intriguing concept that could complement regenerative braking is dynamic wireless charging. This technology would allow electric vehicles to charge while in motion, using charging coils embedded in the road surface.
When combined with regenerative braking, dynamic wireless charging could create a highly efficient energy ecosystem:
- Regenerative braking captures energy during deceleration
- Dynamic charging replenishes energy during acceleration and cruising
- The battery serves as a buffer, storing excess energy and providing power when needed
This synergy could potentially extend the range of electric vehicles indefinitely on properly equipped roads, reducing the need for large, heavy battery packs and further improving overall vehicle efficiency.
Hybrid Energy Storage Systems
Future electric vehicles might employ hybrid energy storage systems that combine different types of energy storage devices to optimize performance. For example:
- High-capacity batteries for long-term energy storage
- Supercapacitors for rapid energy capture during regenerative braking
- Flywheels for mechanical energy storage in certain applications
By leveraging the strengths of each technology, these hybrid systems could maximize the benefits of regenerative braking across a wide range of driving conditions.
Conclusion and Future Outlook
The future of regenerative braking in electric vehicles is bright, with numerous exciting developments on the horizon. From improved energy recovery systems and integration with autonomous driving technologies to advancements in energy storage capabilities, these innovations promise to significantly enhance the efficiency and performance of electric vehicles.
As these technologies mature and become more widespread, we can expect to see:
- Electric vehicles with dramatically increased range
- Reduced environmental impact through improved energy efficiency
- Enhanced driving experiences with smoother, more responsive braking
- Greater integration of vehicles with smart city infrastructure
The ongoing research and development in regenerative braking technology underscore its importance in the evolution of sustainable transportation. As we move towards a future of cleaner, more efficient mobility, regenerative braking will undoubtedly play a crucial role in shaping the vehicles of tomorrow.
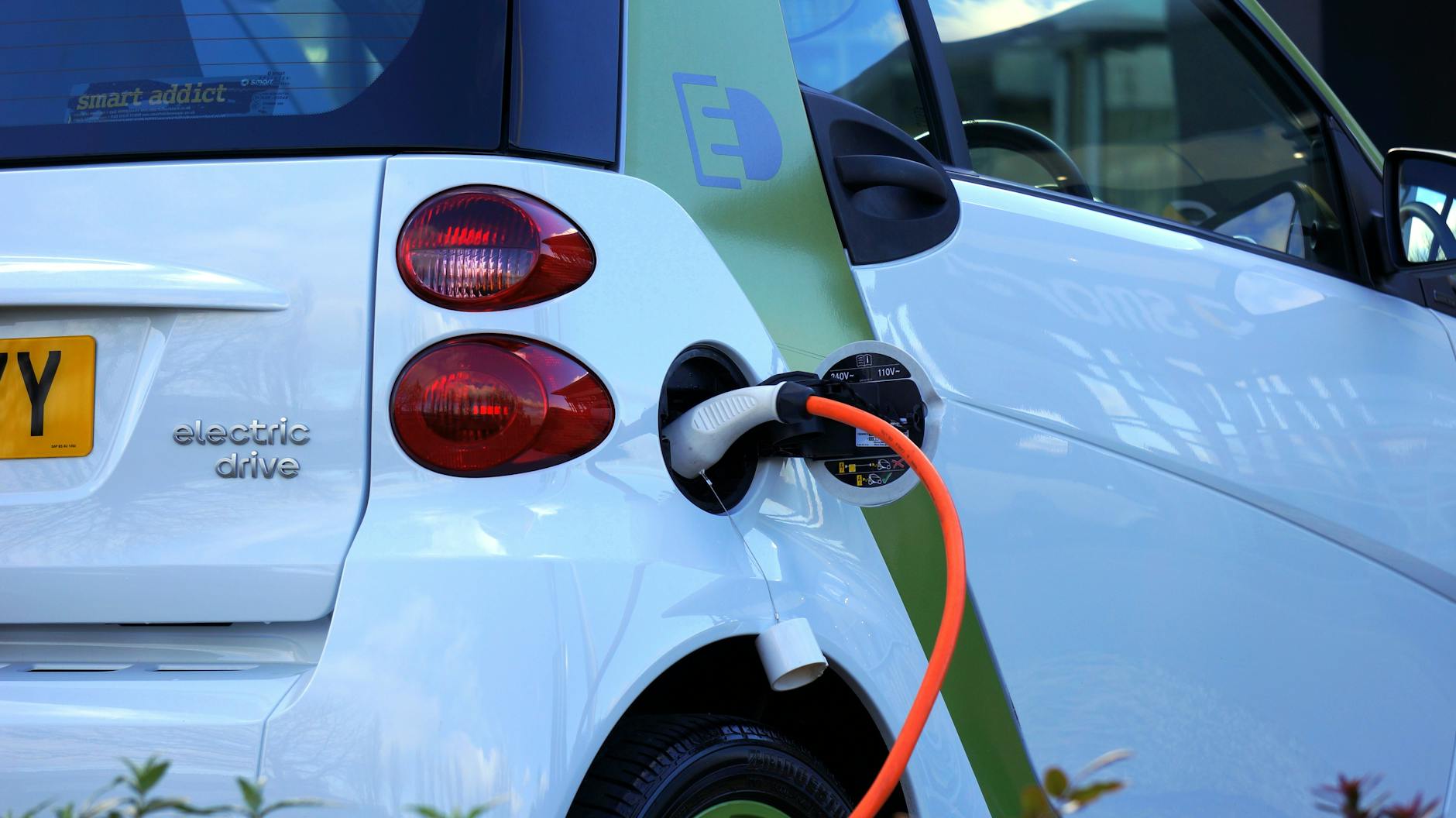
Regenerative braking stands as a cornerstone technology in electric vehicles, offering a clever solution to energy conservation and improved efficiency. By converting kinetic energy into electrical energy during deceleration, this system not only extends the vehicle’s range but also reduces wear on traditional friction brakes. The intricate interplay of motors, batteries, and control systems allows for a seamless transition between acceleration and braking, providing a smoother driving experience.
As we look to the future of sustainable transportation, regenerative braking will undoubtedly play a crucial role. While current systems face challenges such as limited efficiency at low speeds and cold temperatures, ongoing research and development promise to overcome these hurdles. By embracing this technology and supporting its advancement, we can contribute to a greener future where electric vehicles not only consume less energy but also actively recapture and reuse it, making every journey more sustainable.
Leave a Reply